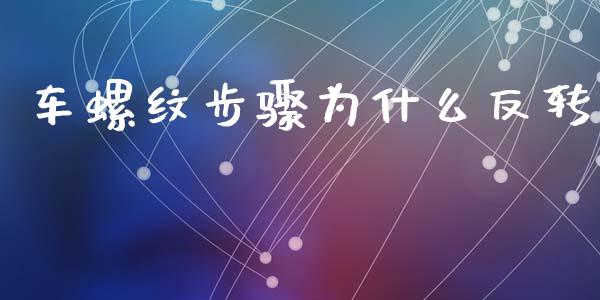
在汽车机械加工中,切削螺纹时经常需要进行操作反转。为什么车螺纹步骤要反转呢?具体原因主要体现在以下三个方面:
保证螺纹精度
在车削螺纹时,刀具的进给方向会影响螺纹的精度。如果刀具沿常规方向进给,即从螺纹外侧向内切削,会产生以下问题:
- 刀具摆动:切削过程中,刀具叶片会因受力不均而产生摆动,导致螺纹牙型不均匀,影响精度。
- 排屑不良:切削过程中产生的切屑会堆积在刀具前端,阻碍切削并导致螺纹表面粗糙。
而当刀具进行反转切削时,上述问题得到解决:
- 刀具稳定:反转切削时,刀具受力方向与摆动方向相反,从而抵消了刀具摆动。
- 排屑顺畅:切屑会随着刀具的逆向运动排出,避免堆积在刀具前端,保障螺纹表面光洁度。
通过反转切削,可以有效提高螺纹的精度。
减少切削力
在常规切削方向下,切削力主要作用在螺纹外侧,这会导致刀具磨损加剧,影响加工效率:
- 刀具磨损:切削力集中在螺纹外侧,会对刀具刃口造成较大的磨损,从而缩短刀具寿命。
- 加工困难:较大的切削力会增加加工阻力,使得刀具难以切入工件,降低加工效率。
而采用反转切削时,切削力主要作用在螺纹内侧,从而减轻了对刀具的磨损,提高了加工效率:
- 刀具耐用:切削力转移到螺纹内侧,减少了刀具刃口的磨损,延长刀具寿命。
- 加工顺畅:较小的切削力降低了加工阻力,使刀具切入工件更加容易,提升加工效率。
优化表面质量
在常规切削方向下,切削刀具会在螺纹外侧形成毛刺和切屑,导致螺纹表面粗糙,影响工件性能:
- 毛刺残留:切削刀具沿顺时针方向切削时,会产生向外翻卷的毛刺,影响螺纹配合精度。
- 切屑附着:切削产生的切屑容易附着在螺纹表面,降低螺纹表面的光洁度,影响工件的密封性能。
反转切削则有效避免了上述问题:
- 毛刺清除:反转切削时,刀具沿逆时针方向切削,会将毛刺推入螺纹内侧,有效消除毛刺残留。
- 切屑排出:切屑会随着刀具的逆向运动排出,减少切屑在螺纹表面的附着,保障螺纹表面光滑。
反转切削可以优化螺纹的表面质量,满足高精度、高光洁度的工件要求。
车螺纹步骤反转的主要原因是:
- 保证螺纹精度:减少刀具摆动,改善排屑,提升螺纹牙型均匀度。
- 减少切削力:将切削力转移到螺纹内侧,减轻刀具磨损,提高加工效率。
- 优化表面质量:消除毛刺残留,减少切屑附着,保障螺纹表面光滑。